Rosyth Dockyard
- Corecut were employed by Babcock Marine to work at Rosyth Dockyard as part of an infrastructure upgrade
- The existing caisson required widening, with a new piece to be welded into place
- The project involved cutting a caisson in two with accuracy to allow for a successful weld
- Wire Sawing was deployed in order to create the most accurate cut
- Hilti Great Britain provided a 50m length of specialist steel diamond wire and a Hilti PR25 Rotating laser fitted to the Wiresaw to aid accuracy
- Due to the structural makeup of the caisson, two cuts were required
- Thanks to our expert staff, the job was completed on time and on budget
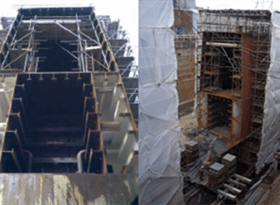
Background
Rosyth Dockyard is a large naval dockyard located on the Firth of Forth at Rosyth, Scotland and is owned by Babcock Marine. This site is primarily used as the integration site for the Royal Navy’s newest aircraft carriers. Corecut were tasked with cutting a huge caisson in two as part of a programme of infrastructure upgrades.
In a dockyard, a caisson performs a similar task to lock gates on a canal, but with the distinction that a caisson is moveable and floats like a ship. When a vessel needs to be dry docked, the dock is first flooded, the caisson is then removed by pumping out the water inside of it.
When afloat it is moved by capstan and cables to the outside wall leaving the entrance to the dock clear. The vessel is then towed into the dock and the caisson is returned to the entrance and guided into position. Water is then pumped into it tanks to sink it and form a watertight seal. It is then used as a walk and roadway. The water in the dock is pumped out, with the vessel being docked on oak blocks at the same time.
The caisson, already around 33m wide, 5.8m deep and 15.5m high, needed to be widened, with a new piece welded in place, so an accurate and clean cut was paramount, requiring the specialist knowledge provided by Corecut operatives.
The wire saw easily handles the thickest sections of all construction materials with cutting rates in excess of 1sqm/hour achievable and the ability to cut circular openings up to 2500 mm
The Project
The project was more complex than simply cutting a caisson in two. The cut had to be accurate enough to allow for a successful weld in so that the structure would remain watertight. The new caisson extension piece had already been prefabricated to fit straight in between the two sections of the existing Caisson and had to be welded without the need for any infill metal.
Hilti helped to put together the cutting concept which included an innovative setup requiring 24 metres of wire and a total steel cutting area of 4024 cm²
PREPARATION
This job required painstaking preparation with adaptations made to existing equipment and test cuts carried out at the Corecut head office development area to ensure that the required cut accuracy, speed of cut and consumable life were within the anticipated parameters and that the method of set up was perfected before arrival. On site, there was a 24 hour setup period involving checking the measurements using the latest laser alignment equipment.
The project was complicated further as the interior of the caisson contained various Ballast Tanks and internal bracing, all of which had to be cut with the same degree of accuracy as well as the Mass Concrete Ballast to the Keel section. The cuts also had to be wedged as the cut progressed to prevent the natural expansion & contraction of the steel affecting the cutting process by snagging the wire.
As this procedure had not been carried out before, a raft of technical documentation and cutting processes had to be produced with the assistance of Hilti Great Britain.
The equipment
Corecut’s Wire Sawing process used a 50m length of specialist steel diamond wire supplied by Hilti. Diamond wire sawing is the fastest and most versatile means of cutting heavily reinforced concrete and steel. The wire saw easily handles the thickest sections of all construction materials with cutting rates in excess of 1sqm/hour achievable and the ability to cut circular openings up to 2500 mm diameter leaving clean straight and smooth cut surfaces with no damage to the remaining structure.
In addition, the Hilti PR25 Rotating Laser which was used to establish that the Diamond Wire was properly aligned with the vertical cuts from top to bottom. A variety of pulley sets were required including an extended telescopic set modified by Corecut to allow the position of the pulley wheels to be adjusted without setting up the pulley every time.
MAKING THE CUT
The structural makeup of the caisson meant two distinct cuts were required. The first one was the lower ballast section of 3.5m high that included concrete and steel. The second, and much larger cut, was of 12m and was completed in one go.
The set up was overseen by Finlay Crocker Managing Director of Core Cut Ltd and Ernst Siegenthaler, Hilti’s Global Key Account Manager of the Diamond Systems Business Unit and carried out in conjunction with engineering staff from the client Babcock Marine. Thanks to the expert staff at Corecut, the job was successfully completed on time and on budget.