Liverpool Seaforth Passage
Summary
- Core Cut Ltd were contracted for preparation work to widen areas of the Port of Liverpool’s Seaforth Passage
- A combination of Wire Sawing and Hydrodemolition were used to clear the path for a new service culvert
- A total of 260t of concrete was removed safely in a cost-effective manner that allowed the busy shipping passage operated as normal
- Using hydrodemolition techniques will more than double the life of any repair or coating when compared with concrete removal using jack hammers
- Using robotic hydrodemolition was the safest and most controlled method of concrete removal and negated the need for any additional temporary works
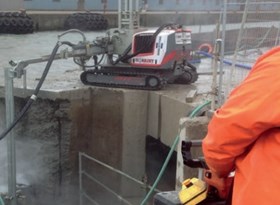
Background
On taking delivery of the UK’s first AQUA CUTTER 710V Evolution robotic Hydrodemolition unit (the 50th globally), British contractor Core Cut Ltd was to play a crucial role in the preparation work for widening the Gladstone Lock entry and the adjacent quayside infrastructure at the Port of Liverpool.
The increasing size of next generation cargo ships calling at the port has resulted in a need to expand the area at Liverpool’s Seaforth Passage and docks. The extra width of the passage will greatly improve turnaround times within the tidal windows.
Belfast-headquartered Farrans Construction secured the contract to carry out the work which will widen the passage by 20m to a total of 60m on completion. It will also see new fendering around the Gladstone Lock port entry, the existing wall demolished and a new quay wall constructed.
Widening works initially required the re-routing of electrical and water services between the quay areas on either side of the Seaforth Passage. It’s here where the ability of Corecut to offer both Wire sawing and Hydrodemolition services as a sub-contractor proved invaluable.
“As part of the passage widening works we have to demolish the existing service culvert. As a result, a service diversion ‘U-Tube’ is being constructed to replace the existing culvert crossing the passage,” explained Farran’s Section Engineer, Ryan Dillon.
In total some 260t of concrete was then removed in around 14 lifts – and all as the busy shipping passage operated as normal around the work.
New Service Culvert
In total, the new ‘U-Tube’ under construction is 120m long. It consists of the risers at either side which are each 20m long, a 70m straight section under the sea bed and a further 10m section at a 60 degree angle around the eastern port side’s horizontal leg.
Fabricated from 1,020mm diameter steel tubes, it will contain a 315mm HDPE water main, six 33kV cables, three 11kV cables and various port comms, all pre-installed as the U-Tube is prefabricated on a separate Quay.
This entire U-Tube structure will be transported from the pre-fabrication yard to the Seaforth Passage via a 250T crane barge before being installed to its final position via a three crane lift.
Before this can be done, however, the receiving locations on both sides of the passage have to be cut out and removed in a controlled manner; in order to protect the integrity of the existing structure and ensure it can be reinstated following the installation of the new U-Tube.
“Pneumatic or mechanical breaking wasn’t an option due to the vibrations it would have induced,” explained Corecut’s Operations Director Ewan Crocker. “Drilling or hand lancing would also have required the erection of
elaborate and expensive scaffolding and the use of man baskets.
“Due to the depth of the sections involved and the restricted working area – with slab depths in excess of a metre – floor and wall sawing and stitch drilling were also ruled out.
“We therefore proposed a combination of Wire Sawing and Hydrodemolition techniques employing the AQUA CUTTER Evolution 710V with its extension arms as a safe, cost effective and time-saving alternative.”
710V Evolution Robot
The 710V Evolution robot is the most versatile Hydrodemolition machine on the market, with the flexibility to work horizontally, vertically and on over-head applications. The unique 3D positioning of the front power head gives the operator full freedom to efficiently reach all areas without limitations.
Wire Sawing allowed Corecut to initially move large sections of concrete from both the receptor locations over areas 3.5 metres wide and 2.5 metres long and also up to 3.5 metres deep.
In total some 260t of concrete was then removed in around 14 lifts – and all as the busy shipping passage operated as normal around the work.
The 710V AQUA CUTTER was then brought in to remove concrete up to 500mm in depth from both end walls to expose the rebar. In total more than 26m² of concrete was safely and efficiently removed from both receptor locations.
A key benefit of the Hydrodemolition process is that it removes the concrete without damaging the rebar, ensuring swift re-concreting onto clear reinforcement once the U-Tube structure is in position.
It is recognised that hydrodemolition techniques will more than double the life of any repair or coating when compared with concrete removal using jack hammers.
Working remotely and largely from the top of the dock walls, Corecut’s robot cut in a trapezoid pattern to remove the concrete, at certain points with the power head – which contains no sensors – working below the water line.
“Robotic Hydrodemolition provided the safest and most controlled solution for this job and the use of the extension arm and small hood allowed it to get at otherwise unreachable sections without the need for any additional temporary works,” says Farrans’ Ryan Dillon.
“It also made it possible to remove the slab which was permanently submerged below dock water level in an accurate and safe manner. The daily yield was very impressive.”
“The AQUA CUTTER can get where other equipment can’t,” added Ewan Crocker.
Once all preliminary work has been completed at the Seaforth Dock, a new quay will be installed and the existing wall demolished. The completion of the overall project is expected to be around February 2015.